Nazarköy craftsman continues ancestral profession
İZMİR
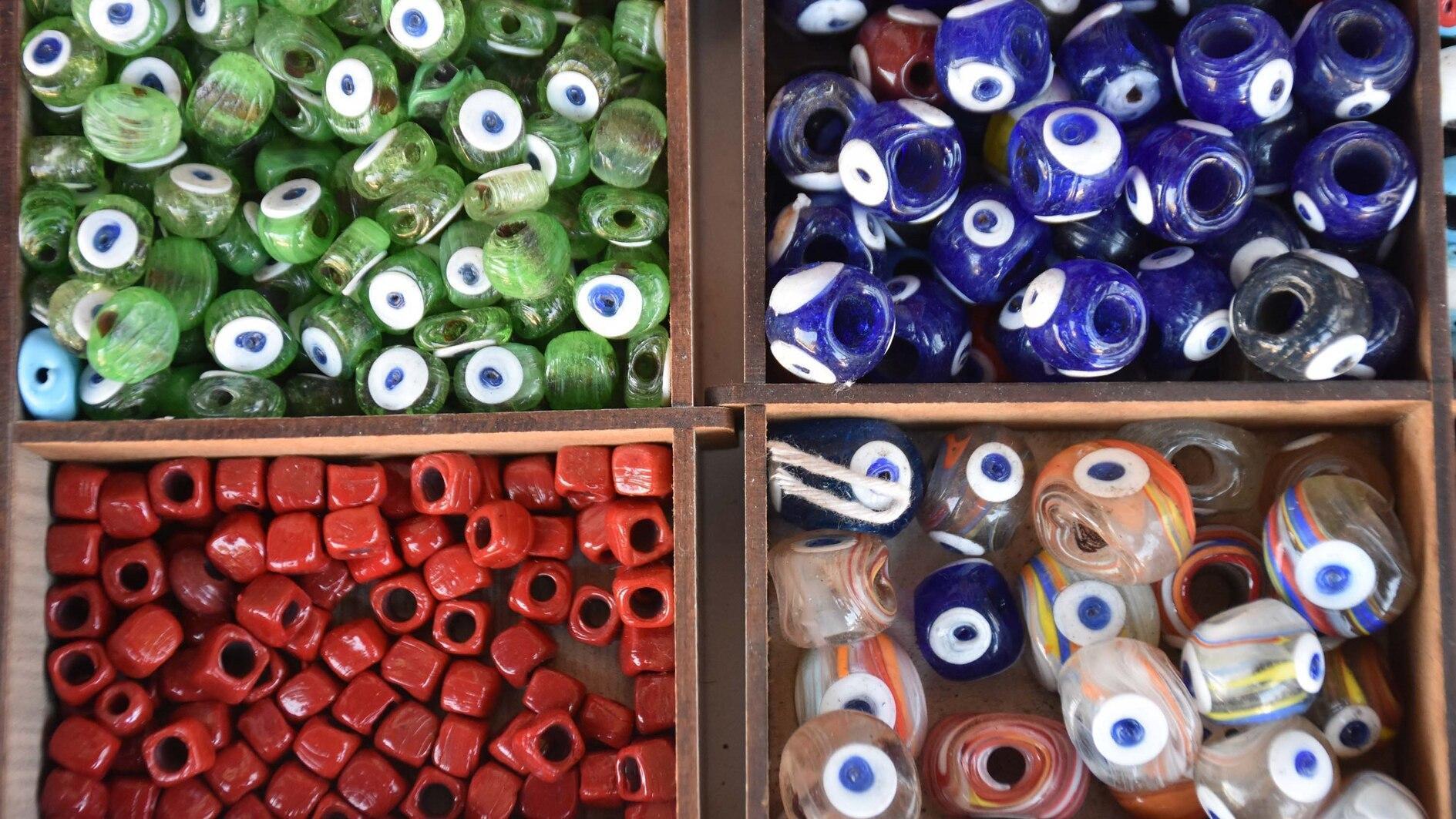
In Nazarköy, a neighborhood in İzmir's Kemalpaşa district, Uğur Karataş, 39, a third-generation craftsman, has been creating glass evil eye beads for 28 years, a skill he learned from his grandfather and father at the age of 11.
Karataş says, “I love this work. We work in front of 1,200-degree heat. Without passion, you can't stand before that fire and continue a craft on the brink of extinction.”
For over 80 years, the sound of iron tools has echoed in Nazarköy, a neighborhood famous for its glass evil eye bead production. Formerly known as Kurudere, the neighborhood was renamed Nazarköy in 2007 due to its long-standing tradition of bead making, which dates back to the mid-1900s. The area is home to numerous workshops and shops.
Born and raised in Nazarköy, Karataş carries on his family’s legacy as a third-generation craftsman. “My father, grandfather, brother-in-law, uncle and older brother all practiced this craft. As children, we pretended to make beads while playing. When my father, grandfather and brothers worked, we would gather around the furnace. In the past, beads were made from recycled bottle glass. We used to clean the bottles. I started this profession at 11, making 'saraç,' round beads without eyes. My late brother-in-law taught me how to add the eye, and my uncle showed me how to shape the molds. Each elder, each master, taught me a different technique,” he explained.
Karataş shared that three brothers of Egyptian origin brought the craft to the village, then called Kurudere, in 1942 and taught it to local masters, including his grandfather.
“Between 1942 and 2005, our village had 18 workshops, and this craft was the village's main livelihood. However, imitation beads made from plastic or acrylic, imported from abroad, caused significant financial losses for artisans. Many masters stopped working because they couldn’t make a living. Although the village's name was changed in 2007 to promote awareness and train new artisans, it didn’t prevent the decline. Today, there are only three active workshops. Normally, five people can work in one furnace, but right now, there are just three of us,” he said.
Men in the village know how to make beads
Karataş, who inherited the craft from his grandfather and father, emphasized the importance of passing the knowledge to future generations. “I hope there will be those who want to learn this craft and carry it forward. This endangered traditional craft must reach the next generations. Around 80-90 percent of the men in the village know how to make beads. Some young people are enthusiastic, saying, ‘I want to learn this.’ We taught them how to hold the iron, shape the mold and create designs. I personally trained six apprentices in the village. One of my friend’s sons is currently learning the technical aspects of the craft from me,” he said.
Karataş noted that traditional glass evil eye beads are on the Culture and Tourism Ministry’s list of protected crafts and have also been added to UNESCO's tentative heritage list.
“There are living human treasures in İzmir working on these beads. The evil eye bead holds great significance in Türkiye. But there’s no younger generation to carry it forward. This is a disappearing craft. While we make a living from it, those who consider learning it often view it purely in economic terms. Imitation beads imported from abroad have deeply hurt our trade. The younger generation doesn’t want to make this their profession. We’re unable to maintain the workforce. Many masters now work in factories. If we could bring them back to the village, we could operate 10 furnaces instead of three,” he said.
Karataş continued, “If the younger generation sees economic value in this craft, they might choose it as a profession. I do this work with love. Without love, you can’t continue a craft that is vanishing.”
Highlighting the importance of raising awareness about traditional glass evil eye beads, Karataş added, “The imported beads have white inner holes, while ours have a rust-like mark from the iron rods used in production. The eyes on our beads also have slight bubbles, showing they’re handmade. We want people to prefer these authentic, handcrafted beads.”