Not just threads but design makes spider webs strong
PARIS - Agence France-Presse
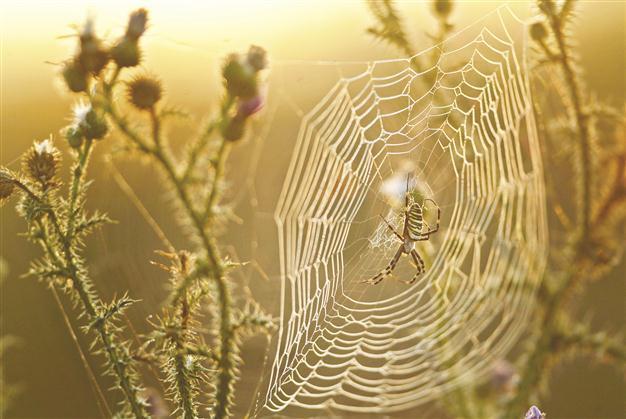
The silk-like threads are famously stronger than steel and tougher than Kevlar. AFP photo
Scientists said Feb. 1 that they had unraveled the mystery of how spider webs can withstand multiple tears and even hurricane-force winds without collapsing. The findings should be of keen interest to engineers searching for shock-resistant structural designs, they said.The silk-like threads with which arachnids spin their traps are famously stronger than steel and tougher than Kevlar, but this alone does not explain how webs withstand, say, a gash from a fallen branch. Once ripped, what keeps the whole web from falling apart?
Researchers probed the question using lab experiments, observation and computer modelling. They began by delving deeper into the molecular structure of the silk threads. A strand comprises a unique combination of shapeless protein and ordered, nanoscale crystals, they found.
When stress increases -- the falling branch, for example -- the filament elongates in four phases: a linear tugging, a drawn-out stretching as the protein unfolds, a stiffening phase that absorbs force, and finally the breaking point triggered by friction.
Spider threads fall into two categories, and what makes webs so resilient is how they interact, the researchers said. So-called viscid silk -- stretchy, wet and sticky -- winds out in ever-widening spirals from the center of the web, and serves to capture unsuspecting prey. But the straight threads that radiate outwards like spokes on a wheel, called dragline silk, are dry and stiff and provide structural support. The radial and spiral filaments each play a different role in absorbing motion, and the way they are intertwined limits puncture damage to the spot where it occurs, the researchers found.